Palowanie, pale fundamentowe, mikropale
Wznoszenie nowych obiektów budowlanych każdorazowo wiąże się z problematyką właściwego wykonania ich fundamentów. Zwiększająca się świadomość zarówno osób profesjonalnie związanych z budownictwem jak i samych inwestorów w zakresie należytego wykonania fundamentów obiektu powoduje, że coraz rzadziej mamy do czynienia z błędami pojawiającymi się na tym etapie procesu budowlanego.
Wykonanie fundamentów pośrednich w postaci mikropali czy pali przenoszących obciążenia na warstwy nośne położone głębiej daje pewne oparcie i minimalizuje ryzyko niekontrolowanych osiadań, przechyłów czy pęknięć konstrukcji.
Pale fundamentowe można podzielić na dwa podstawowe rodzaje:
- Pale gotowe (drewniane, stalowe, żeliwne, żelbetowe, itp.).
- Pale wykonywane w miejscu budowy (betonowe lub żelbetowe).
Pale wiercone świdrem ciągłym CFA
Pale CFA (Continous Flight Auger) zwane również FSC (Formowane Świdrem Ciągłym) to wiercone pale fundamentowe wykonywane przy zastosowaniu świdra ciągłego na całej długości odwiertu. Bardzo popularna technologia palowania, która znalazła swoje zastosowanie zarówno w klasycznych konstrukcjach jako typowe nośne pale fundamentowe ale również przy wzmacnianiu podłoża, stabilizacji osuwisk i wykonywaniu ścian zabezpieczających głębokie wykopy.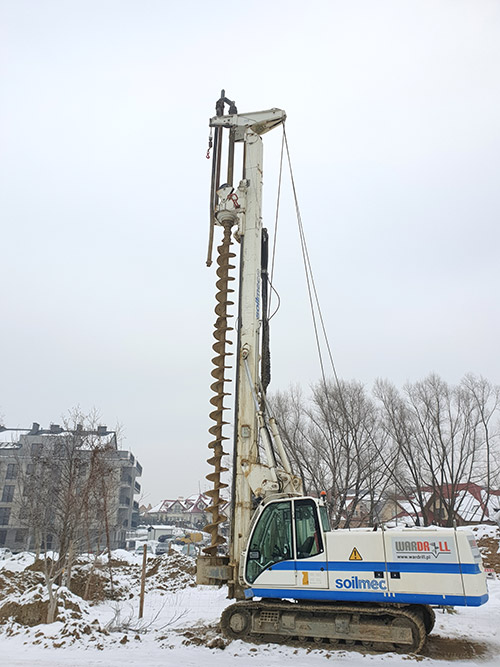
- Zasadnicze wiercenie pala świdrem ślimakowym. Długość zastosowanego świdra powinna w tym przypadku być sumą: głębokości wiercenia i długości roboczej zależnej od parametrów zastosowanej palownicy. Świder podczas wiercenia osiąga rzędną wymaganą zgodnie z przyjętym projektem. Grunt podczas wiercenia jest częściowo wynoszony na powierzchnię a częściowo rozpychany na pobocznicy pala.
- Podciąganie świdra z jednoczesnym ciśnieniowym wypełnianiem przestrzeni trzonu pala mieszanką betonową. Świder ślimakowy jest zbudowany w ten sposób, że wewnątrz posiada rurę, przez którą podawany jest beton. Ciśnienie wytwarzane przez pompę do betonu powoduje, że podawana ilość betonu zazwyczaj przekracza objętość geometryczną pala 10% do nawet 40%. Taki sposób formowania pala poprawia jego nośność zarówno w podstawie jak i na pobocznicy.
- Oczyszczenie betonu w strefie głowicy pala. Czynność ta ma na celu właściwe przygotowanie głowicy i ułatwienie procesu zbrojenia pala.
- Wprowadzanie zbrojenia pala. Jest to proces zależny od przyjętego założenia projektowego i w elementach nie obciążonych siłami poziomymi często pomijany. Zbrojenie powinno być wprowadzone w mieszankę świeżą na głębokość wymaganą projektem palowania.
Pale przemieszczeniowe
(FDP – Full Displacement Piles, SDP – Soil Displacement Piles, CMC – Controlled Modulus Columns)
Pale (kolumny) przemieszczeniowe to pale wiercone wykonywane przy zastosowaniu specjalnie ukształtowanego świdra roboczego. Świder przemieszczeniowy zbudowany jest z rury rdzeniowej zakończonej elementem wiercącym o odpowiedniej budowie. Końcówka (nawiertka) wiercąca składa się z trzech elementów: części odpowiedzialnej za wiercenie, części rozpychającej i części utrwalającej wykonany odwiert. Jest to technologia zbliżona do pali CFA, jednak w tym przypadku nie następuje wynoszenie gruntu na powierzchnię. Całość gruntu przez odpowiednie uformowanie świdra jest rozpychana na boki powodując jego dogęszczanie.W procesie wykonywania pali przemieszczeniowych można wydzielić następujące etapy:
- Wiercenie pala na żądaną głębokość. Dolna część świdra roboczego rozluźniając grunt, przy zapewnieniu dodatkowego nacisku pionowego przez palownicę, powoduje zagłębienie się narzędzia. Środkowa część świdra rozprowadza i dogęszcza grunt na pobocznicy w efekcie czego uzyskuje się odwiert o wymaganych parametrach.
- Unoszenie świdra przy jednoczesnym jego obrocie. Specjalnie uformowana górna część świdra (płaty ustawione są przeciwskrętnie do płatów części dolnej) pozwala na dodatkowe przemieszczenie gruntu na boki. Równocześnie z podnoszonym świdrem powstały otwór wypełnia się ciśnieniowo betonem formując trzon pala.
- Oczyszczenie betonu w strefie głowicy pala. Czynność ta ma na celu właściwe przygotowanie głowicy i ułatwienie procesu zbrojenia pala.
- Wprowadzanie zbrojenia pala. Jest to proces zależny od przyjętego założenia projektowego i w elementach nie obciążonych siłami poziomymi często pomijany. Zbrojenie powinno być wprowadzone w mieszankę świeżą na głębokość wymaganą projektem palowania.
Pale wielkośrednicowe wiercone w rurze osłonowej
Jest to powszechnie znana i stosowana metoda wykonywania pali wierconych. Obecnie na rynku wykonuje się pale w rurze osłonowej o średnicach od 600mm do 1800mm. Możliwe jest dodatkowo zwiększenie średnicy podstawy pali poprzez zastosowanie specjalistycznego narzędzia – rozwiertaka oraz wykonanie iniekcji podstaw pali. Poprzez zwiększenie średnicy pala uzyskuje się wyższe parametry nośności. Zastosowanie iniekcji podstaw pali dodatkowo zapewnia ograniczenie osiadań pali.Etapy wykonywania pali wierconych w rurach osłonowych:
- Zasadnicze wiercenie pala przy zastosowaniu wymiennych narzędzi wiertniczych z jednoczesnym zagłębianiem rury osłonowej. W zależności od rodzaju i stanu gruntu stosuje się odpowiednio ukształtowane świdry: ślimakowe, kubłowe czy rdzeniowe, montowane na wieloczęściowej, rozkładanej żerdzi wiertniczej. Urobek z pali jest wybierany z otworu i odkładany na powierzchni. Równocześnie zagłębia się rurę osłonową zapewniającą stateczność pobocznicy odwiertu. W przypadku występowania wód gruntowych, zwłaszcza w gruntach przepuszczalnych, konieczne jest zapewnienie odpowiedniego balastu słupem wody lub specjalnej zawiesiny.
- Przygotowanie dna odwiertu pala. Po osiągnięciu wymaganego poziomu, dno odwiertu należy właściwie oczyścić. W przypadku wykonywania poszerzenia podstawy, wykonuje siego na tym etapie.
- Umieszczenie konstrukcji szkieletu zbrojeniowego w wykonanym otworze. Jeżeli założono konieczność wykonania iniekcji podstaw pali, zbrojenie powinno być wyposażone w przewody i dysze iniekcyjne.
- Betonowanie trzonu pala z równoczesnym wyciąganiem rur osłonowych. Beton podawany grawitacyjnie przez rurę kontraktorową.
- Skucie głowic pali po stwardnieniu mieszanki.
- Wykonanie ewentualnych iniekcji podstaw pali.
Iniekcja podstaw pali wielkośrednicowych
Przeprowadzenie iniekcji strefy dolnej pali ma na celu zapewnienie równomiernej pracy pali i minimalizację ich osiadań. Dodatkowo wzmocnienie gruntu pod podstawą pala zwiększa jego opór w tej strefie i sprawia, że mobilizacje oporu podstawy i pobocznicy wyrównują się. Zabieg ten podnosi zatem nośność pala i sprawia, że ewentualne błędy wykonawcze, popełnione na etapie odwiertu pala (rozluźniona podstawa, brak właściwego przygotowania dna odwiertu) zostają wyeliminowane.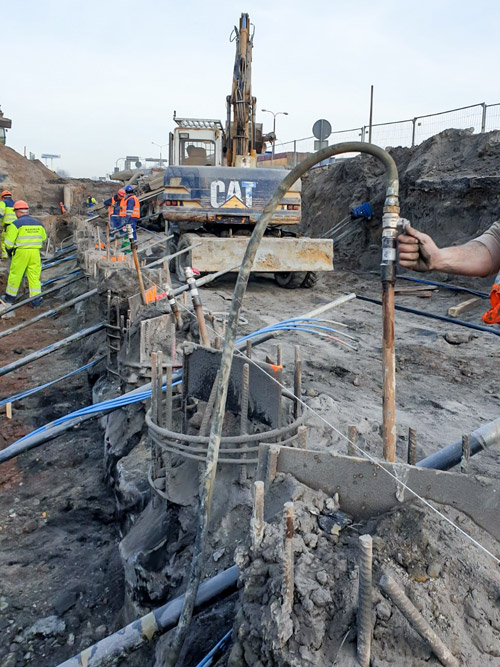
Roboty przygotowawcze
Instalacja do tłoczenia zaczynu iniekcyjnego mocowana jest do zbrojenia pala i składa się z dyszy iniekcyjnej wykonanej z elementu rury w części poziomej w podstawie pala oraz pionowych rur tłoczących zaczyn iniekcyjny. W dyszy iniekcyjnej wykonuje się w co najmniej trzech miejscach otwory o średnicy Ø8 mm osłonięte specjalnymi opaskami gumowymi zabezpieczającymi przed powrotem iniektu do instalacji.
Roboty iniekcyjne
Do robót iniekcyjnych przystępuje się po min. siedmiu dniach od daty zabetonowania pala. Iniekt wykonuje się na bieżąco na budowie przy wykorzystaniu specjalnego mieszalnika. Następnie przy użyciu pompy iniekcyjnej iniekt wtłaczany jest do przygotowanej instalacji. Przed przystąpieniem do robót należy sprawdzić drożność instalacji. Zaczyn należy wprowadzać z małym wydatkiem i stale kontrolować parametry tłoczenia.
Parametry podlegające kontroli:
- Przemieszczenie pala – najważniejszy parametr, którego przekroczenie mogłoby ujemnie wpłynąć na nośność pala (naprężenia krytyczne na pobocznicy pala). Przemieszczenie nie może przekroczyć 5,0 mm. Po osiągnięciu tej granicy iniektowanie należy automatycznie przerwać.
- Ciśnienie – zwiększane jest stopniowo (4 stopnie co 0,3 MPa) utrzymując każdy stopień przez minimum 5 min a ostatni stopień 10 min. Maksymalne ciśnienie stosowane do iniekcji zależy od wielu warunków, między innymi od przemieszczenia pala i składu iniektu.
Po uzyskaniu maksymalnego ciśnienia roboczego zabieg należy zakończyć. Maksymalne ciśnienie robocze nie powinno przekraczać 1,5 MPa. - Skład i dawka iniektu – kontrolowany jest stosunek c/w oraz przerwy pomiędzy kolejnymi tłoczeniami jak również przyrost ciśnienia przy kolejnych tłoczeniach. Nie należy tłoczyć więcej niż 500,0 litrów iniektu pod jeden pal w ciągu 24h.
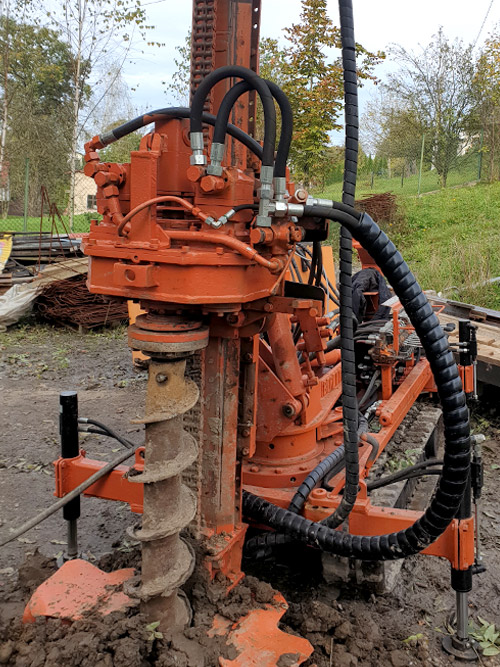
Mikropale wiercone świdrem ciągłym CFA
Mikropale CFA to mikropale wiercone z zastosowaniem świdra ciągłego zazwyczaj o średnicy 200mm do 300mm. Zasada działania jest zbliżona do typowych pali CFA, różnica polega na zastosowaniu dużo mniejszych wiertnic i innego czynnika roboczego w postaci iniektu cementowego. Miniaturyzacja sprzętu do palowania pozwala na wykonanie tego typu pali w przestrzeniach ograniczonych jak: piwnice, wąskie pomieszczenia, miejsca z utrudnionym dojazdem.Proces wykonywania pali CFA dzieli się na następujące etapy:
- Wiercenie pala świdrem ślimakowym. Długość całkowita świdra powinna zapewnić odwiert na pełną długość pala. Grunt podczas wiercenia jest częściowo wynoszony na powierzchnię a częściowo rozpychany na pobocznicy pala.
- Podciąganie świdra z jednoczesnym ciśnieniowym wypełnianiem odwiertu iniektem cementowym. Zaczyn iniekcyjny o odpowiednich parametrach podawany jest w sposób ciągły przez zestaw pompy iniekcyjnej i mieszalnika. Poprzez ciśnieniowe podawanie iniektu nośność pobocznicy pala wzrasta.
- Oczyszczenie betonu w strefie głowicy pala. Czynność ta ma na celu właściwe przygotowanie głowicy i ułatwienie procesu wbudowania zbrojenia pala.
- Wprowadzanie zbrojenia pala w świeży zaczyn cementowy na głębokość wymaganą projektem palowania. Opcjonalne wyposażenie zbrojenia pala w przewody do iniekcji.
- Opcjonalne wykonanie iniekcji podstaw lub pobocznicy mikropala poprzez przytwierdzone do zbrojenia przewody iniekcyjne wyposażone w specjalne dysze.
Mikropale iniekcyjne
Mikropale iniekcyjne to pale o średnicach do 300mm i długościach typowych do ok. 10,0m. Z uwagi na technologię wiercenia można rozróżnić dwie podstawowe metody wykonywania mikropali: - mikropale tradycyjne - mikropale samowiercące
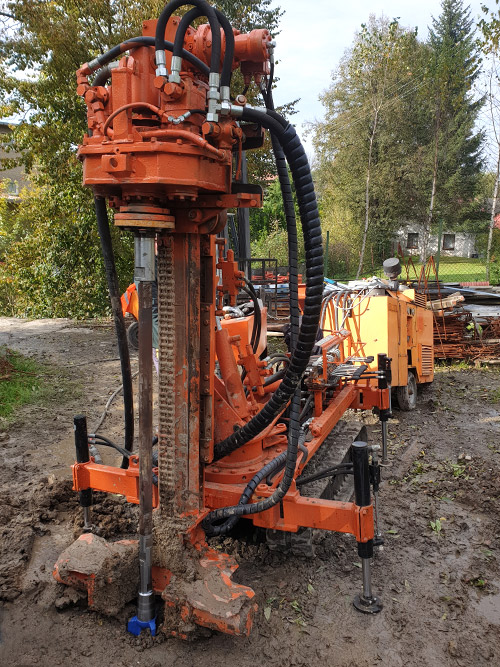
W metodzie tej stosuje się narzędzia wielokrotnego użytku. Wiercenie, w zależności od rodzaju gruntu, wykonywane jest: na sucho, w rurze osłonowej lub płuczce zapewniającej stateczność otworu. Zastosowanie płuczki umożliwia, oprócz stabilizacji otworu również transport zwiercin na powierzchnię. Parametry płuczki powinny być tak dobrane by uniknąć negatywnego wpływu zarówno na ściany otworu jak i zabudowywane zbrojenie mikropala. Do zalet mikropali tradycyjnych należy zaliczyć: ekonomiczność rozwiązania, możliwość dodatkowego zwiększenia nośności pali poprzez zastosowanie wieloetapowych iniekcji, zmniejszenie ryzyka uszkodzenia zbrojeń oraz możliwość zastosowania dodatkowych zabezpieczeń antykorozyjnych zbrojeń, możliwość kontroli parametrów gruntu podczas wiercenia. Do wad natomiast zaliczyć należy: większą czasochłonność wykonania, zwiększona ilość stosowanego sprzętu wiertniczego.
Mikropale samowiercące
Mikropale w tej metodzie wykonywane są przy zastosowaniu specjalnego zestawu traconych żerdzi wiertniczych zakończonych koronką wiertniczą. Wiercenie odbywa się w osłonie z zaczynu cementowego głowicą udarowo-obrotową. Poprzez zastosowanie takiego rozwiązania cały cykl wykonania mikropala realizowany jest w jednym etapie – jednoczesne wiercenie, zabudowanie zbrojenia i formowanie trzonu iniektem. Zaletami tego systemu są: szybkość wykonania, możliwość zastosowania sprzętu małogabarytowego. Wadami natomiast są: brak możliwości wieloetapowej iniekcji, mniejsza skuteczność iniekcji pierwotnej poprzez podawanie iniektu „od dołu” i zastosowanie układu „otwartego” wiercenia, ograniczenia w zastosowaniu zabezpieczeń antykorozyjnych żerdzi wiertniczych.